Individual Project | 15 Weeks | 2017
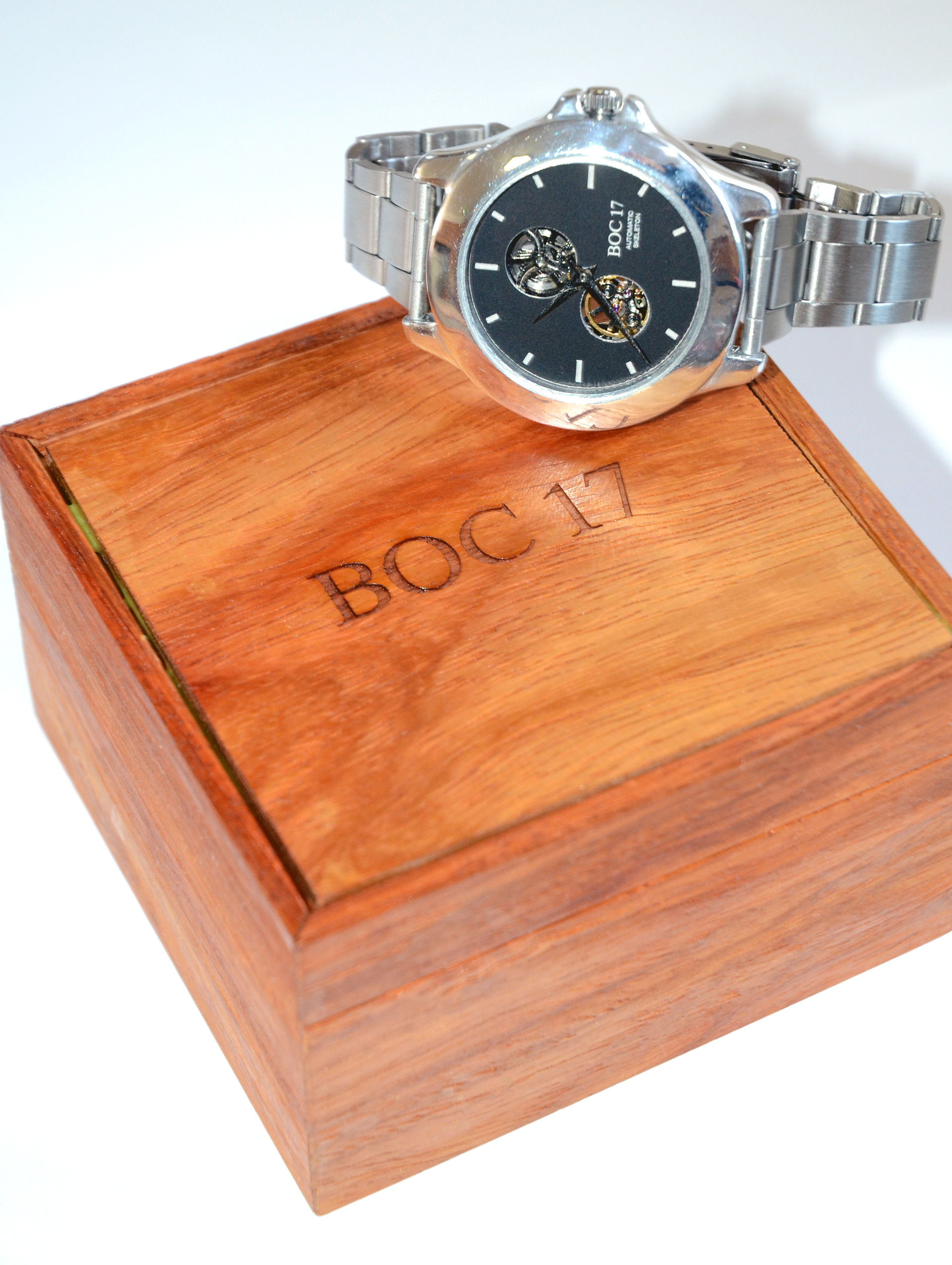
Brief
To design a personalised watch for the Technology Studies subject.
Process
A considerable degree of market research and analysis was undertaken prior to any design work. Vigorous concept generation and exploration was carried out. Aesthetic and materials research was undertaken. Extensive CAD modelling was undertaken to arrive at the final design. An immense amount of prototyping and user testing was done to ensure all the components fit within the watch assembly. This lead to the manufacture of the final prototype which was heavily hands-on and required a lot of manual labour. Manufacture of the watch case was done by CNC milling aluminuim. Manual post-processing and refinement was carried out. The watch dial was laser etched and cut to size. A leather watch strap was sewed by hand and the housing box was also custom made.
CAD model assembly made in Autodesk Inventor.
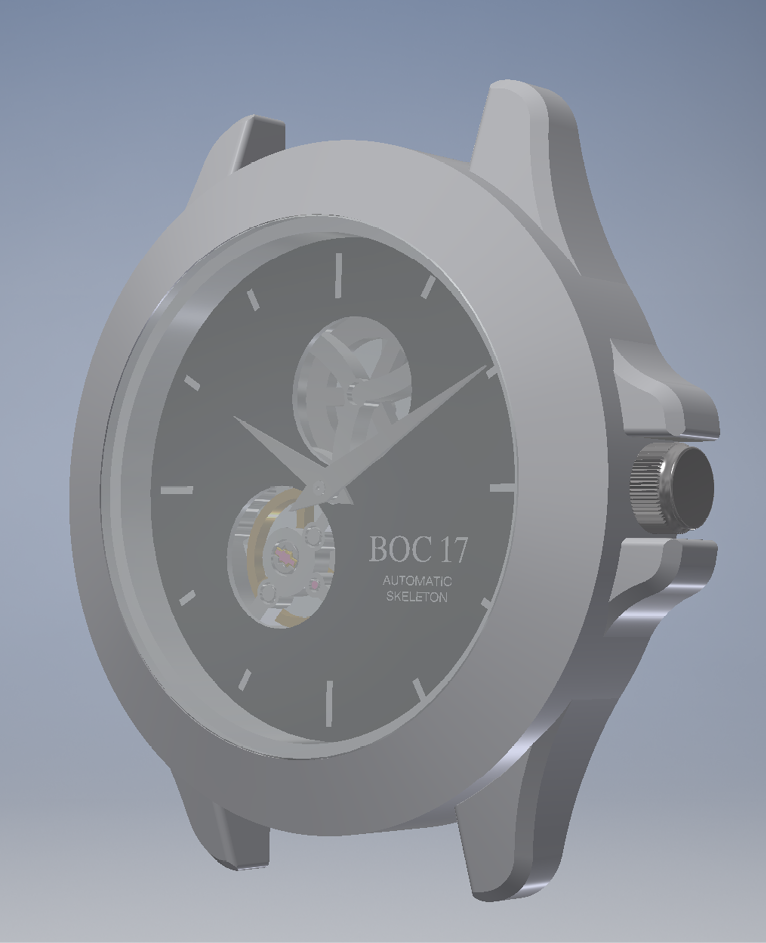
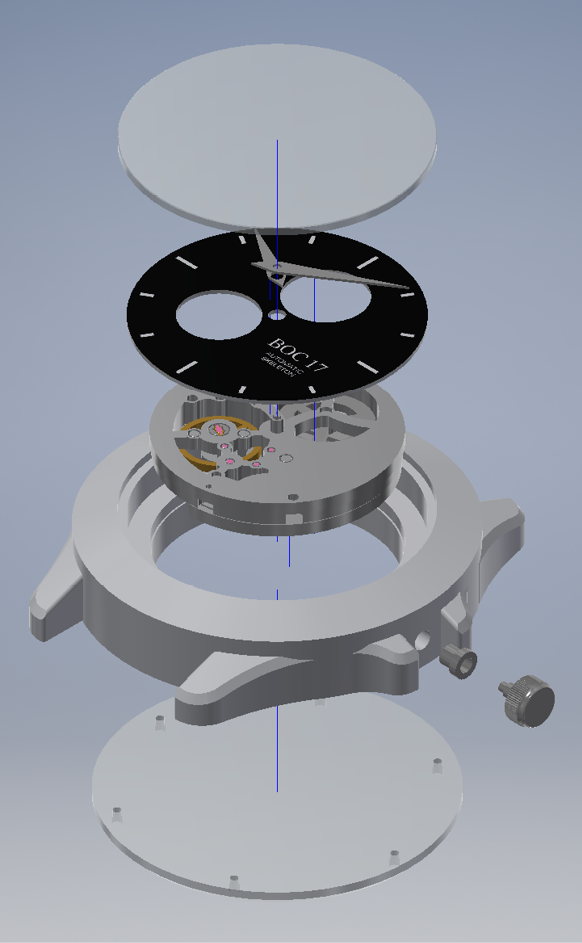
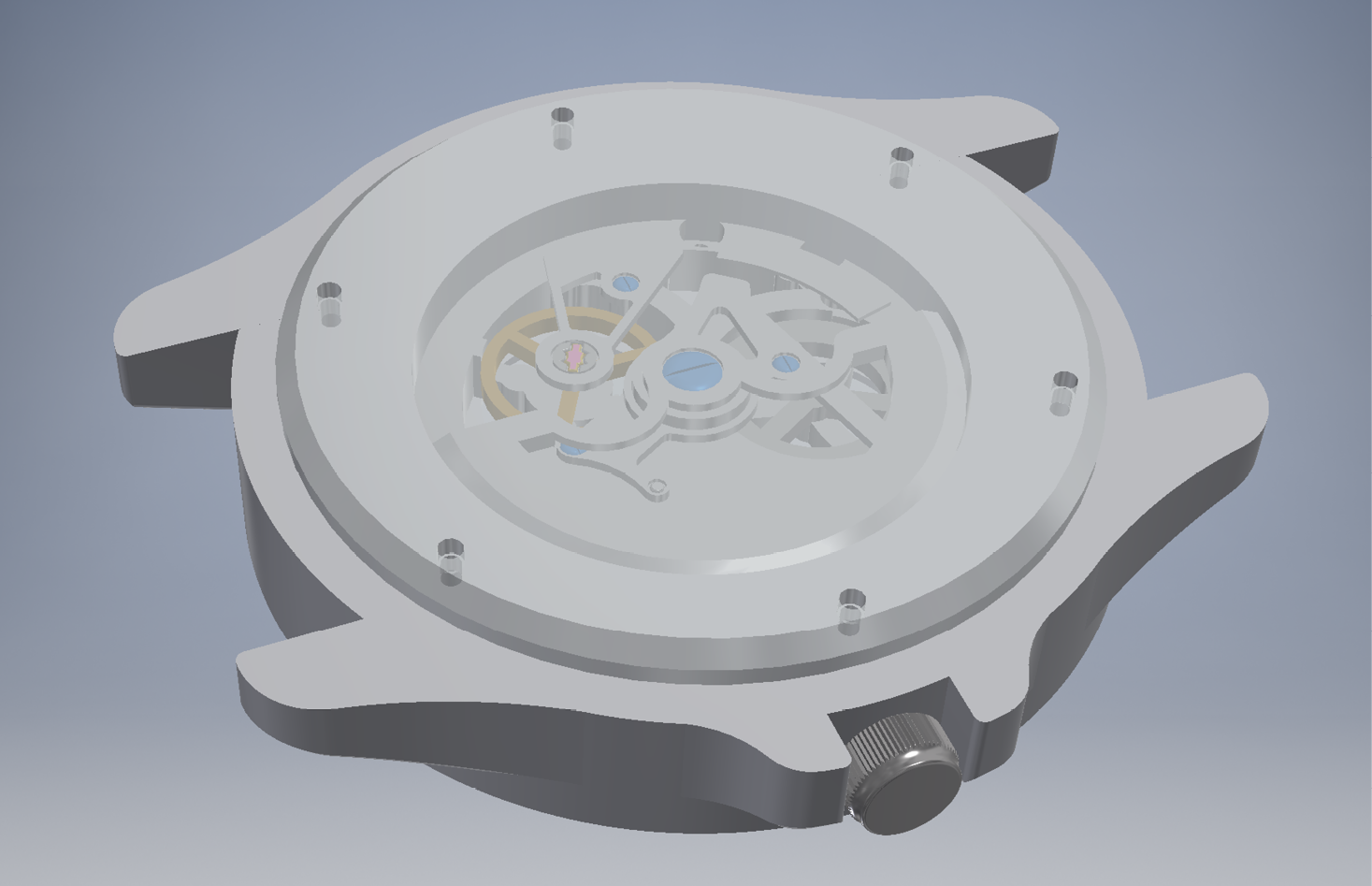
The watch case was CNC milled from an aluminium block. The CNC mill used was 2-axis.
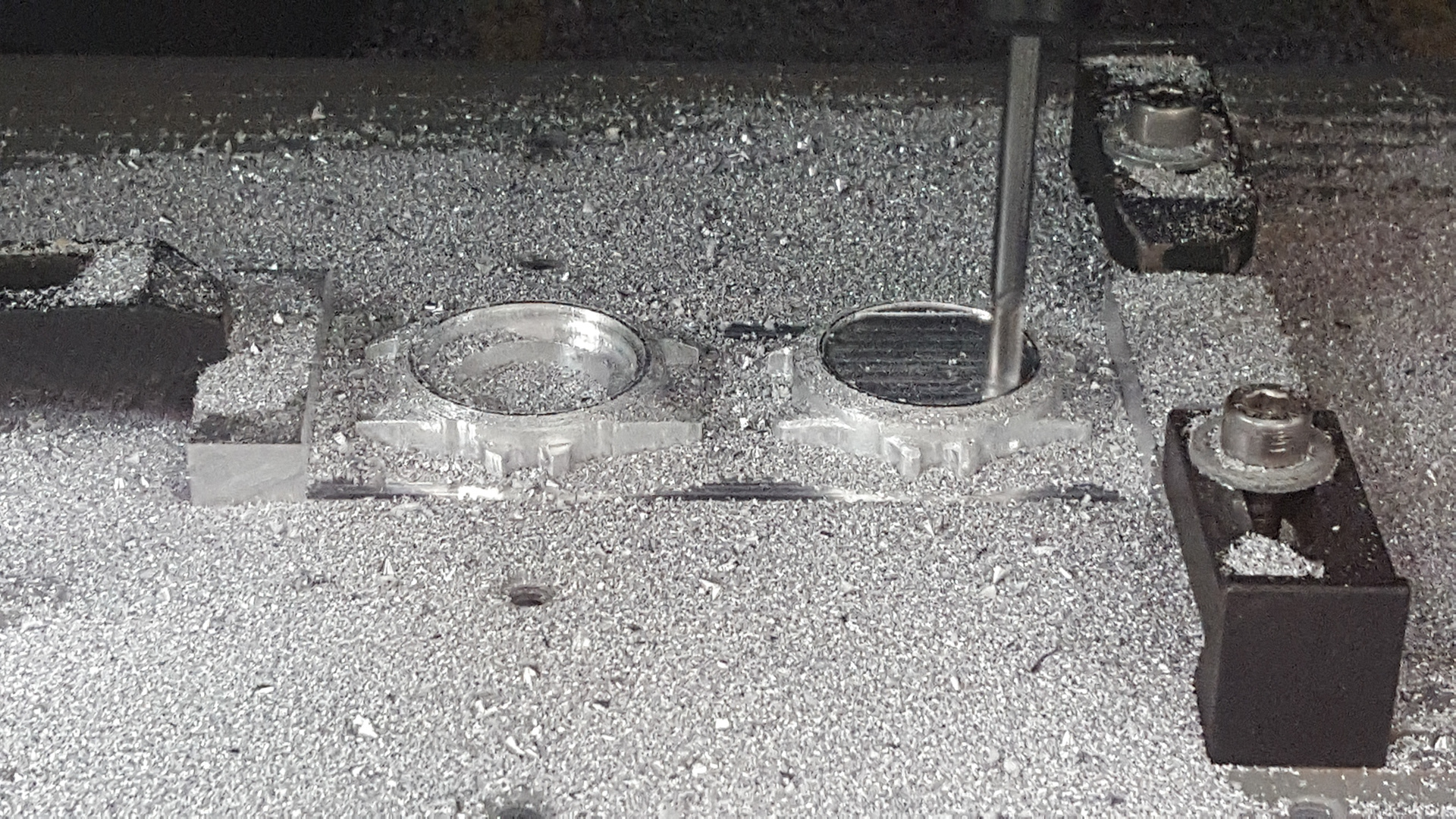
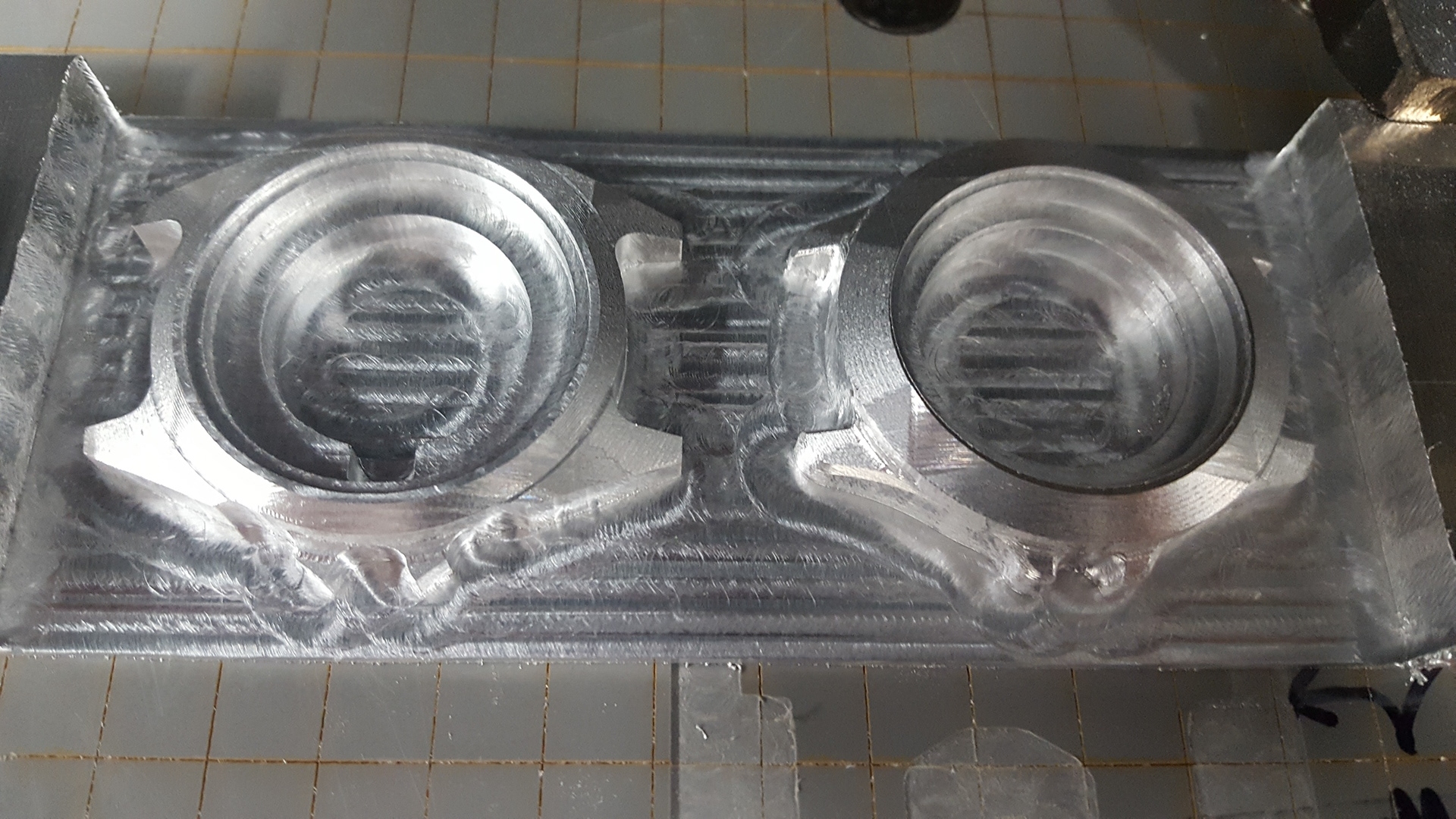
After the case was milled, extensive manual post-processing including cutting off excess material with a band saw, wet and dry sanding with various machinery, and polishing.
The watch dial was laser etched onto anodised aluminium and cut to shape.
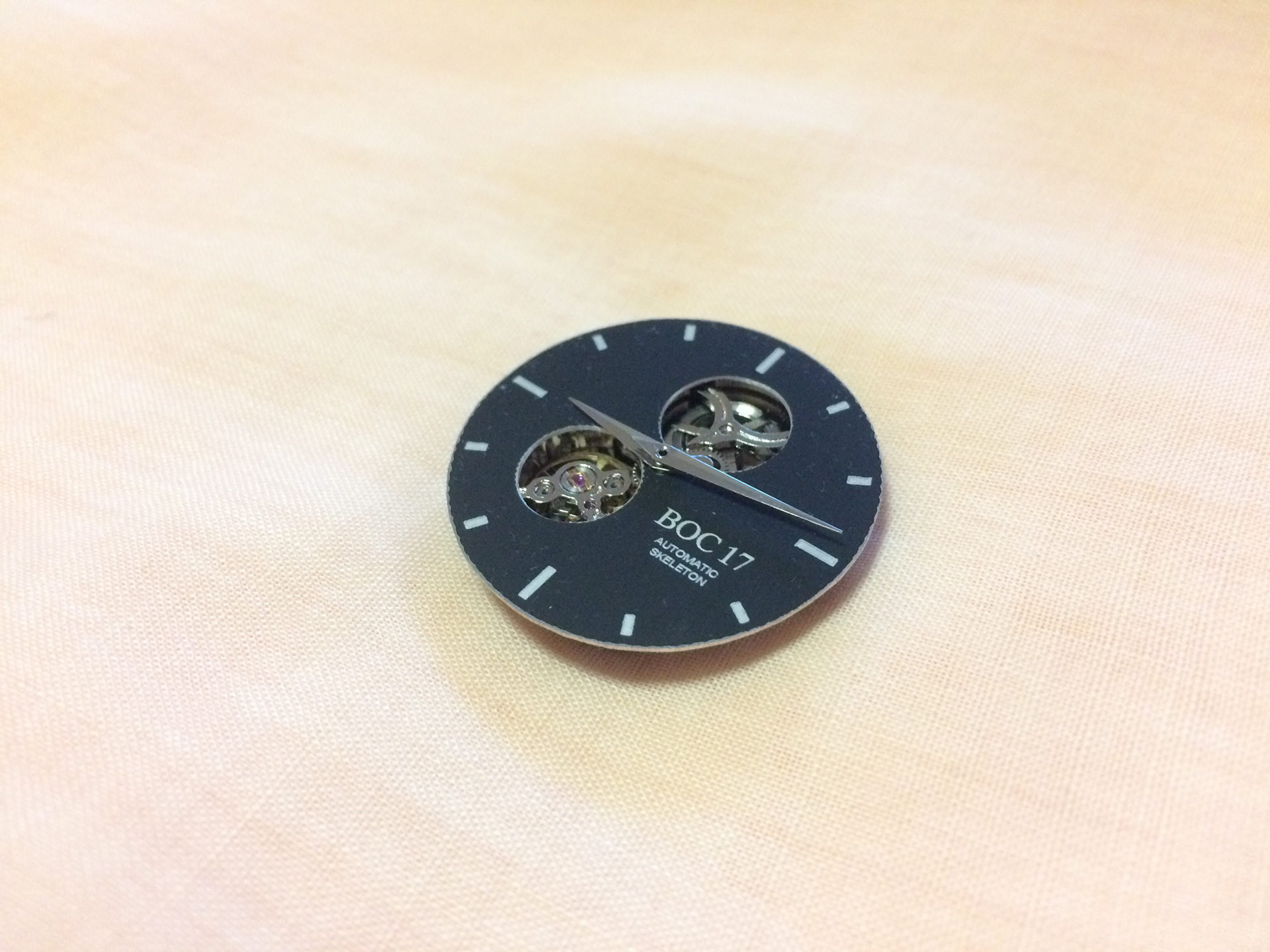
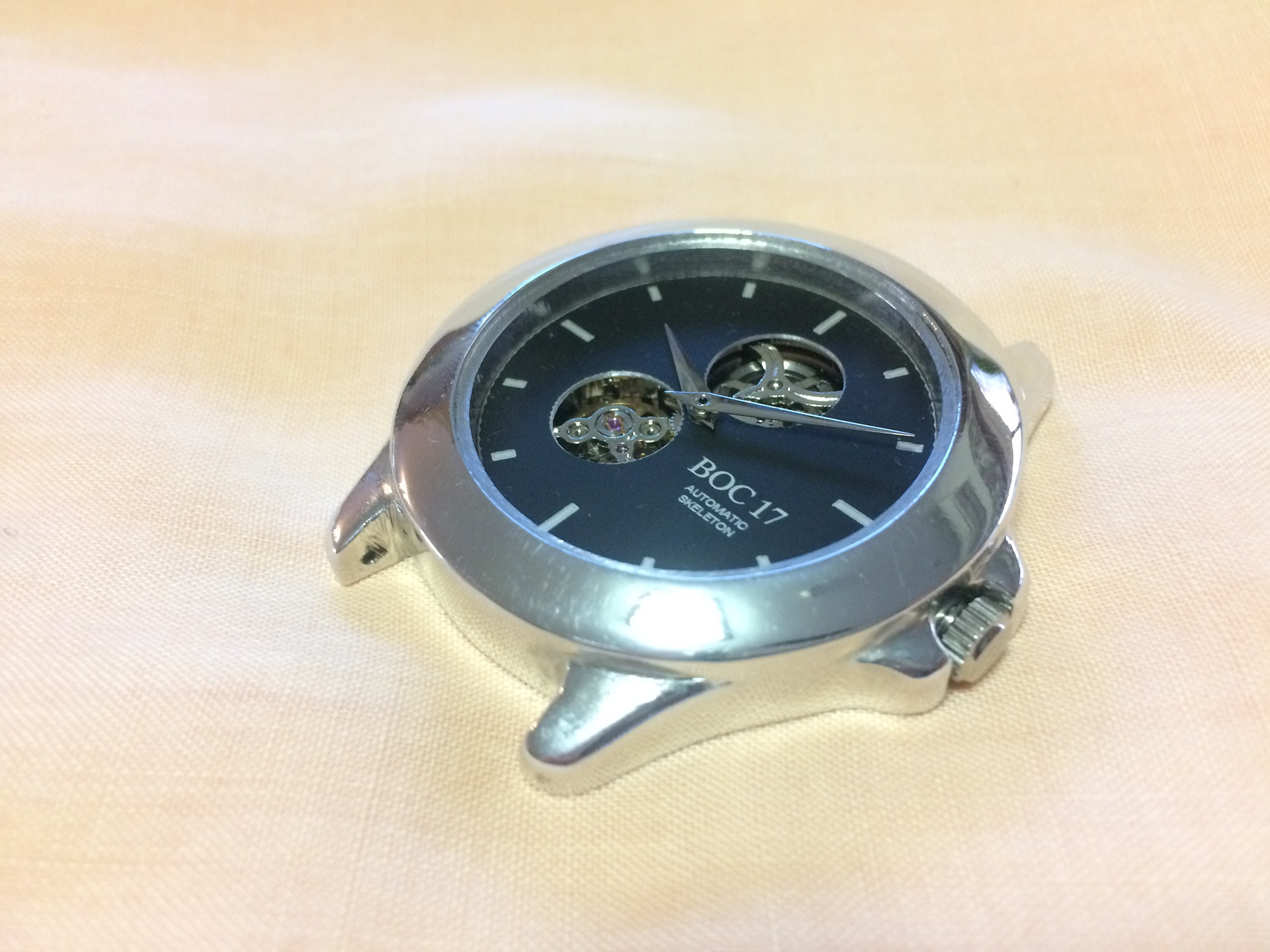
The caseback is made from laser cut acrylic and the screw holes were tapped manually.
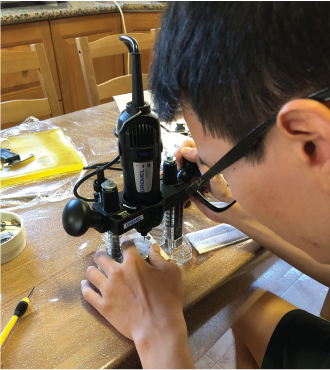
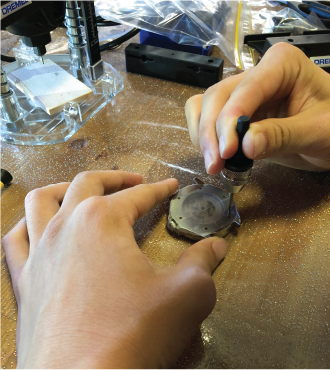
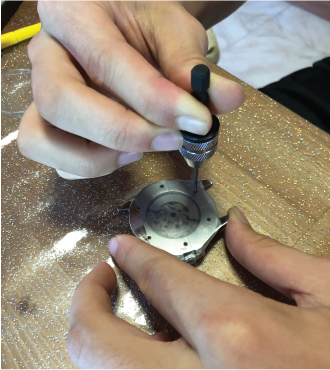
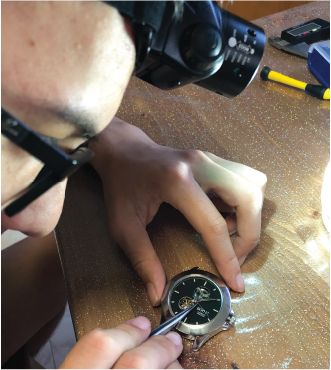
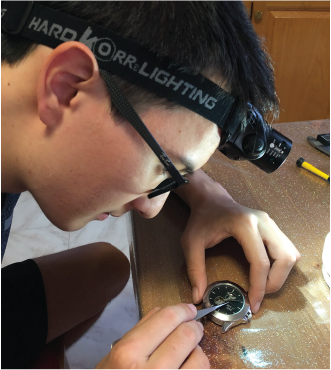
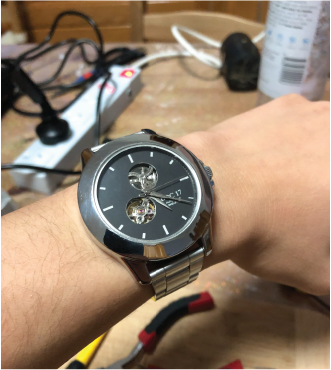
To accompany the watch, I made a custom housing box and hand-sewed watch strap.
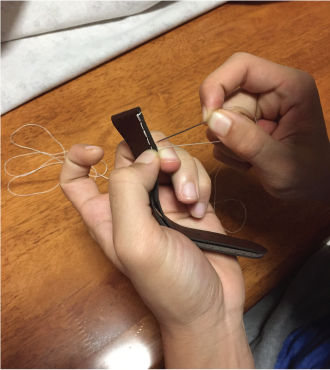
Design
The watch features an automatic skeleton movement and was designed as an opened heart watch. Two watch cases were made from the design; one was made from aluminium and the other stainless steel. At the time of this project our facilities at school only allowed for soft metals, plastics, and timber to be CNC milled. During the semester I worked on completing a working prototype made from aluminium however, a stainless steel case was made for the final product (this was completed outside of school dates).
The watch dial was custom made from anodised aluminium and the time increments were laser etched using a laser cutter. The holes to expose the mainspring and balance wheel were cut using a dremel. The box that houses the watch was also custom made along with a secondary watch strap which was hand sewed from kangaroo hide.
I achieved the highest grade in my cohort for Technology Studies and received an award for my academic and design efforts.
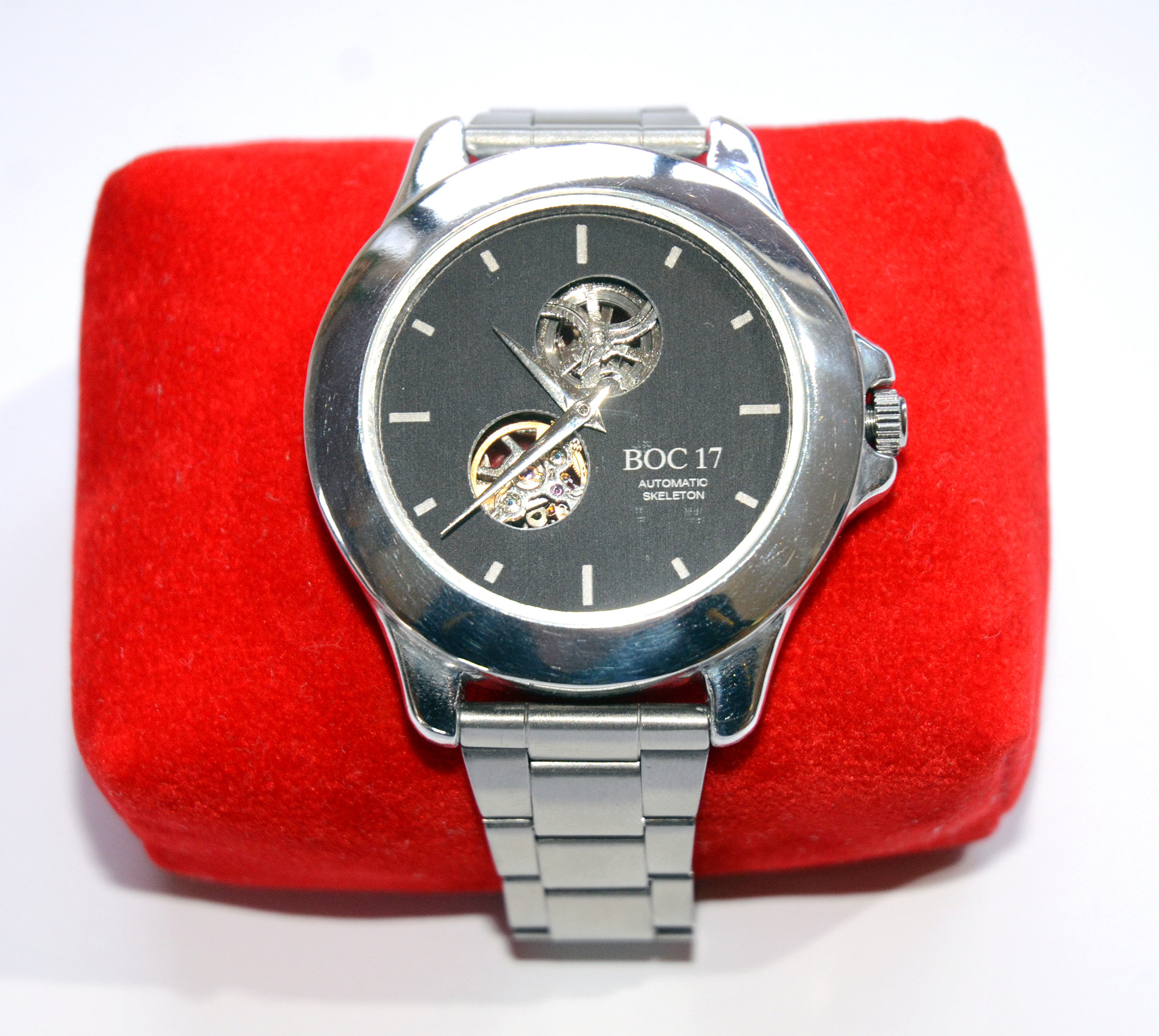
Watch is an open heart design which exposes the balance wheel and mainspring

Clear caseback to expose the automatic skeleton movement
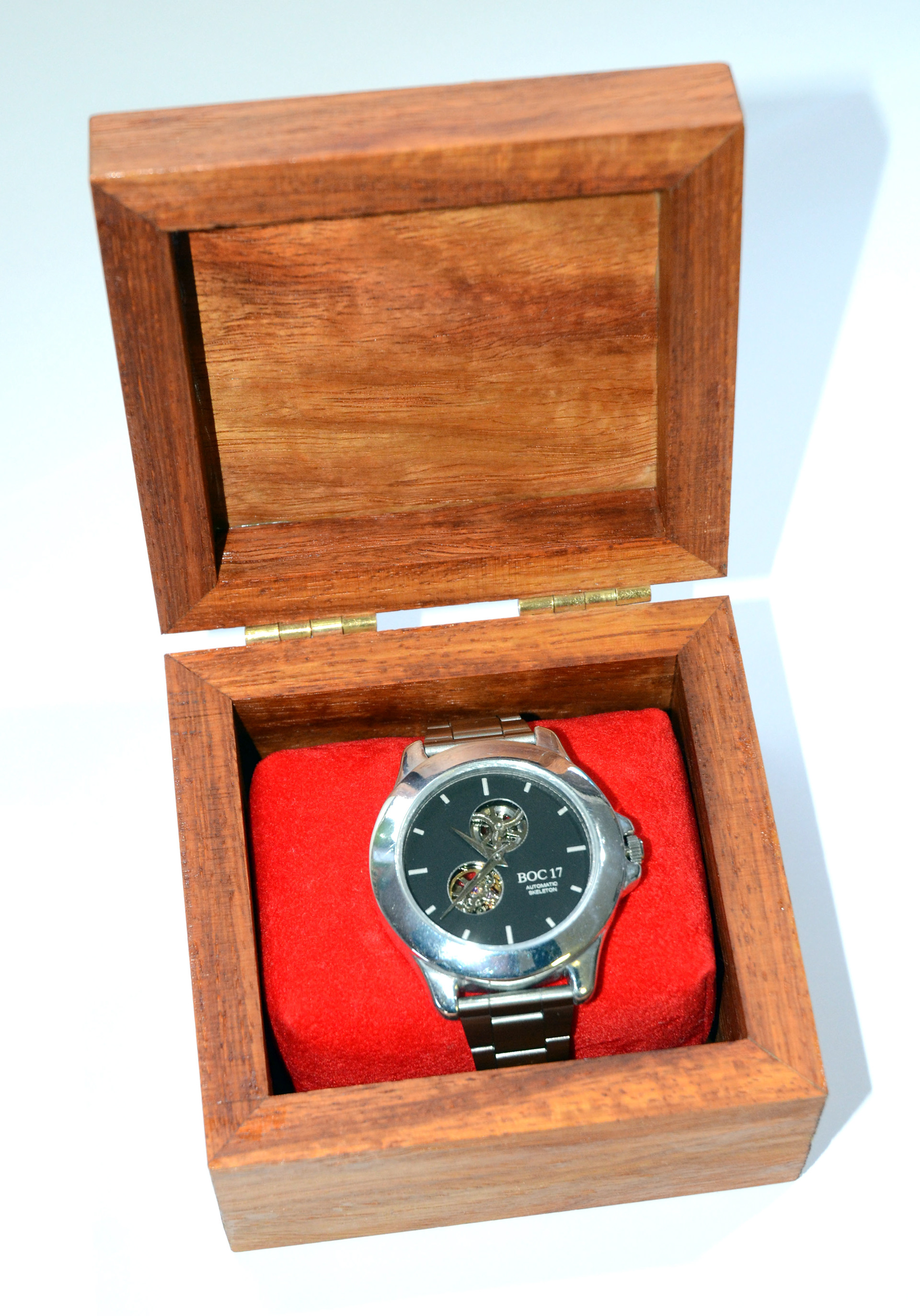
Personal watch in custom box
Software
The only program used to produce the final design was Autodesk Inventor.